O corte a laser permite produzir peças mais complexas e precisas, com uma junta de corte mínima, menor influência de calor e maior qualidade de corte.
Principais motivos que levam o Laser a ser um doa mais avançados sistemas de corte de chapas :
- Cantos com qualidade
- Não causa distorção nas peças
- Mínima camada de influência térmica
- Redução nos custo da peça
- Menos sucata
- Ciclo rápido de produção de amostras
- Processa uma grande variedade de espessuras
- Flexibilidade e versatilidade
- Trabalho sem danos na superfície das peças
- Sistema permite operar com peças já puncionadas
Fonte: http://www.lgvcortelaser.com.br/servicos.htm#cortejatoagua
http://sazi.plugin.com.br/laser/produto_detalhe.asp?CodProduto=96
http://www.aga.com.br/international/web/lg/br/likelgagabr.nsf/DocByAlias/app_cw_laser_cut
O corte com jato de água puro e com jato abrasivo é efetuado atualmente por sistemas totalmente automatizados tipo CAD/CAM. O sistema usado é o Modelo 2652A da OMAX, que foi adquirido com o apoio da Fundação de Amparo a Pesquisa do Estado de São Paulo - FAPESP, constituindo o Módulo de Jato Abrasivo da EPUSP[2].
O sistema consta de uma bomba de ultra-alta pressão, uma mesa XY para suporte do material alvo de corte e movimentação do bocal e um sistema de controle constituído de um computador. A bomba de alta pressão do modelo acima é de 30 KW (20HP), e fornece uma pressão da água da ordem de 290 MPa (42.000 psi). A mesa XY é dotada de um grande tanque de água para coleta dos detritos gerados no corte dos materiais sendo retangular e têm uma área útil de corte de 665,6 mm (26 polegadas) por 1.331,2 mm (52 polegadas) donde provem os números do modelo. Existem sobre a mesa, dois cursores orientados por deslocamentos de precisão através de duas guias. Na extremidade do cursor X está preso o bocal cujo trajeto pode ser feito para qualquer parte da área de corte. O sistema de controle é realizado através de computador, onde um desenho em CAD (Desenho com Auxílio de Computador arquivo de terminação .dxf) após convenientemente ordenado, é executado por CAM (Manufatura auxiliada por computador) no sistema. Em síntese, o desenho é feito na tela, e o computador o corta através de um "plotter". Como inicialmente referido o corte pode ser feito com jato de água pura, ou com jato de água abrasivo. Existem para isso dois bocais distintos que são o de água pura, e o de água com abrasivos. As figuras 1a e 1b mostram estes esquemas.
No bocal de água pura Figura 1a), a saída da água ocorre através de um orifício em jóia (rubi ou safira), cujo diâmetro está entre 0,3556 mm (0,014 polegada) e 0,254 mm (0,010 de polegada), a qual está localizada na extremidade do bocal.
No bocal de injeção (Figura 1b) a jóia está alojada mais acima, tendo associado um tubo de mistura ou de foco.
A câmara de mistura é constituída pelo tubo de foco, que possui uma entrada cônica e por um espaço adicional. Através da câmara de mistura é que se dá a entrada do abrasivo. O líquido gerado no orifício da jóia possui uma velocidade de aproximadamente 3 vezes a do som (cerca de 800 m/s) e passa pelo centro do tubo de mistura sugando o abrasivo. Tal mistura é direcionada no tubo antes de atingir o material alvo a ser cortado (vide Figura 1b).
O abrasivo normalmente empregado nestes sistemas é um mineral chamado granada. No presente estudo foi empregada a granada importada da Flow de 80# cujas características tecnológicas podem ser encontradas em artigo divulgado em 2000 em evento na Grécia[3].
Assim, é possível efetuar o corte de praticamente qualquer material com até 170 mm de espessura (ou mais, dependendo do equipamento) em uma única operação, com qualidade de bordas, sem necessidade de acabamento posterior.
O corte com jato de água, pura ou com abrasivo, é um processo a frio e corta por erosão, com alta precisão e qualidade de acabamento.
Abaixo estão algumas peças cortadas com o sistema Jato de Água.
Titânio

Cobre

Material Misto

Polímeros

Aço
Fonte: http://www.lgvcortelaser.com.br/servicos.htm#cortejatoagua
· O corte por cisalhamento;
· Uma região fraturada com ruptura por tração;
· Uma rebarba.

A profundidade de penetração depende da ductilidade e espessura do material a ser cortado. Quanto mais dúctil o metal a ser cortado, maior a penetração da faca. Contudo, metais dúcteis e muito macios(especialmente chapas finas) tendem a curvar-se na operação de corte por cisalhamento resultando em grande volume de rebarba.
A qualidade do corte por cisalhamento depende fundamentalmente da qualidade das facas de corte e da regulagem das folgas entre as facas.
Equipamentos que cortam por cisalhamento:
Guilhotinas
Tipos de guilhotinas:
· Mecânica – Executa corte em chapas de aço sobre um traçado ou com uso de limitador mecânico(stop) chamado de encosto, incorporado à máquina. O conjunto de potência de uma guilhotina mecânica é constituído por motor, volante, coroa sem fim acionada pelo volante e uma embreagem que liga a coroa sem fim ao eixo e além de um mecanismo acionado pelo pedal.
Sua capacidade de corte é para chapas com espessuras inferiores a 13mm e comprimento de até 3000mm.
· Hidráulica – Apresentam cursos mais longos que as guilhotinas mecânicas. São acionadas por um conjunto moto-bomba que força o óleo para dentro do cilindro empurrando o pistão. O movimento do pistão aciona o mecanismo que sustenta a faca superior. As guilhotinas hidráulicas são projetadas com capacidade de carga fixa. Não devem ser cortados materiais que superem a capacidade de corte do equipamento.
Sua capacidade de corte é para chapas com espessuras até 25mm e comprimentos de até 4000mm.
· Pneumática – Usadas exclusivamente para chapas finas de 1,2mm de espessura por 1500mm de comprimento
Tesouras
Tipos de tesouras:
· Manual – Ferramenta manual que executa os mesmos movimentos de uma tesoura de costura. Largamente empregada em caldeirarias e serralherias, na execução de corte em chapas finas(inferior a 1,2mm) e de pequenas dimensões(até 300mm). Não deve ser utilizada em corte de barras e tubos.
· Vibratória manual – Ferramenta elétrica ou pneumática manual que executa os mesmos movimentos de uma tesoura de costura. É adequada a cortes de chapas finas(inferior a 1,2mm) de pequenas dimensões(até 300mm). É uma máquina versátil, podendo cortar peças planas em vários formatos, permitindo a execução de peças especiais. Ela não exige esforço físico do operador, sendo necessários cuidados e habilidade para não sair fora do traçado.
· Vibratória universal – Máquina tipo “pescoço de cisne” para cortes em chapas finas(inferior a 3,0mm). Corta de maneira semelhante à tesoura de uso doméstico, com movimentos alternativos automáticos de vai e vem da faca superior. Executa cortes pequenos ou grandes, circulares ou retilíneos em qualquer ponto da chapa.
Corte por abrasão
O corte por abrasão é executado pela fricção de uma ferramenta de corte no material a ser cortado. Neste tipo de corte, são arrancadas partículas do material a ser cortado(“cavacos”) com conseqüente aumento da temperatura da zona cortada. Quando a espessura da peça a ser cortada é muito grande, existe a necessidade de serem utilizados fluidos de refrigeração. Este tipo de corte pode ser executado por dois tipos de equipamentos: Serras e discos abrasivos.
Corte por serras
Os aços inoxidáveis podem ser cortados por todos os tipos de serras, manuais e mecanizadas. Recomenda-se o uso de lâminas de corte de aço – rápido para qualquer tipo de equipamento. O corte é efetuado em movimentos de vai e vem com amplitude e velocidade adequadas, com o retorno em vazio para evitar um rápido endurecimento da superfície a ser cortada. Recomenda-se o uso de lubrificante(óleo para serviços pesados solúvel em água, dentre outros) para qualquer tipo de serra utilizada, exceto para o caso de serra de fita de fricção de alta velocidade.
Tipos de serras
· Serra manual – Utilizada para corte de peças finas e serviços não repetitivos. Recomenda-se lâminas de 32 dentes por polegada para peças com até 1,60mm de espessura e de 24 dentes por polegada para material com espessura compreendida entre 1,60 e 6,35mm de espessura. Para espessuras maiores, recomenda-se utilizar lâminas de dentes grossos para facilitar a remoção dos cavacos e prevenir entupimento.
· Serra mecânica – Utilizada para cortes de seções relativamente grossas em trabalhos repetitivos ou não. O emprego de equipamento motorizado permite cortes mais profundos por amplitude de curso e requer o emprego de lâminas com dentes mais longos, usualmente de
· Serra de fita – Largamente utilizada para corte de aços inoxidáveis austeníticos. Executa cortes retos ou com contorno irregular tanto em chapas quanto em barras e tubos. O emprego de lâminas de aços rápidos possibilita maior durabilidade e a utilização de velocidades de corte maiores. O corte em materiais trabalhados a frio, deverá ser executado em velocidades menores.
Corte por discos abrasivos
Para a seleção do disco de corte mais adequado, deve-se considerar o tipo de material a ser cortado, a seção do corte, o acabamento desejado e os equipamentos de corte disponíveis(corte refrigerado ou a seco)
Tipos de máquinas de corte por abrasão:
· Cut-off – São máquinas elétricas ou manuais, portáteis ou não. Tem capacidade para discos com diâmetros entre 250 e 400mm.
· Oscilante – Este tipo de máquina é equipada com mecanismo complementar. Além de apresentar movimento de penetração no corte, apresenta também um movimento oscilante em outro sentido dentro de um plano horizontal. Admitem uso de discos entre 350 e 850mm de diâmetros. Tem capacidade de corte de barras de até 300mm de espessura.
· Horizontal – Estas máquinas, além do movimento de penetração do disco sobre a peça, apresentam um movimento para frente e para trás ao longo do corte no plano horizontal. Admitem discos com diâmetros entre 300 e 350mm e servem para cortar vidro e materiais não metálicos. Sua capacidade de corte é de pequenas seções, menores ou igual a 10mm
· Rotativas – Nestas máquinas, além de girar o disco de corte, a peça também é girada. Utiliza discos de dimensões pequenas entre 300 e 350mm de diâmetro. Sua capacidade de corte de peças sólidas ou tubos é de até 550mm de diâmetro.
Corte por fusão
Corte à plasma.....
http://www.losinox.com.br/downloads/aco_inox_manual_conformacao.pdf
Invariavelmente, as operações de soldagem são precedidas pelas operações de corte. Por questões de economia de escala e características do processo de fabricação dos materiais metálicos, estes são produzidos em dimensões padronizadas, não sendo adequadas ao uso para todos os fins a que se destinam. Em função deste aspecto, tornam-se necessárias operações de corte das matérias primas. O corte pode ser efetuado de diversas formas:
• Mecanicamente: Corte por cisalhamento através de guilhotinas, tesouras, etc.; por arrancamento através de serras, usinagem mecânica, etc
• Por fusão: Utilizando-se como fonte de calor um arco elétrico ex. arc air (goivagem), plasma
• Reação química: Onde o corte se processa através de reações exotérmicas de oxidação do metal, ex. corte oxicombustível
• Elevada concentração de energia: Neste grupo enquadram-se os processos que utilizam o princípio da concentração de energia como característica principal de funcionamento, não importando se a fonte de energia é química, mecânica ou elétrica. Enquadram-se neste, o corte por jato d'água de elevada pressão, LASER e algumas variantes do processo plasma
Definição
O oxicorte é o processo de secionamento de metais pela combustão localizada e contínua devido a ação de um jato de Oxigênio, de elevada pureza, agindo sobre um ponto previamente aquecido por uma chama oxicombustível.
EQUIPAMENTOS DO PROCESSO DE OXICORTE
Uma estação de trabalho deve ter no mínimo os seguintes equipamentos para execução do processo:
Um cilindro ou instalação centralizada para o Oxigênio (O2).
Um cilindro ou instalação centralizada para gás combustível (Acetileno, Propano, GLP).
Duas mangueiras de alta pressão para condução dos gases, eventualmente três se utilizar o Oxigênio de corte e de aquecimento em mangueiras separadas.
Um maçarico de corte.
Um regulador de pressão para Oxigênio.
Um regulador de pressão para acetileno.
Dispositivos de segurança (válvulas anti-retrocesso).
MAÇARICO DE CORTE
O maçarico de Oxicorte mistura o gás combustível com o Oxigênio de aquecimento, na proporção correta para a chama, além de produzir um jato de Oxigênio de alta velocidade para o corte.
Este equipamento consiste de uma série de tubos de gás e válvulas de controle de fluxo dos gases Oxigênio e combustível. A figura abaixo mostra um maçarico de corte.

· Cabeça - Proporciona rigidez ao conjunto, e serve de acoplamento aos bicos de corte.
· Tubos - tem a função de conduzir os gases
· Punho - local onde se fará o manuseio do maçarico
· Alavanca de corte - O seu acionamento atua sobre a válvula do O2 de corte proporcionando a abertura do mesmo.
· Conjunto de regulagem - É um conjunto de válvulas que servem para regulagem dos fluxos de gases.
TIPOS DE MAÇARICO
Os maçaricos de corte podem ser manuais, combinado e específicos, ou tipo caneta para acoplamento em máquinas de corte automáticas.
· Maçarico Manual Combinado

É utilizado em locais ou setores onde existe uma alternância entre operações de corte e soldagem tais como oficinas de manutenção.
Neste caso acopla-se a um maçarico de soldagem um dispositivo de corte, ilustrado na figura ao lado, composto por uma câmara de mistura, sistema de separação e válvula para controle do O2 de corte.
· Maçaricos Manuais Para Corte
Possuem um circuito especial de O2 separado dos gases para chama de aquecimento. Este conduto é específico para o Oxigênio que efetuará o corte, passando a se denominar O2 de corte.
A mistura dos gases para chama de aquecimento pode se dar por três princípios distintos que são apresentados à seguir:
· Injetor
O gás combustível é succionado através da alta velocidade do Oxigênio por meio de um venturi.
· Misturador
Os gases comburente e combustível chegam à câmara de mistura com pressões iguais através da regulagem das válvulas.
Fonte: www.metalica.com.brPorém, existem aplicações que os outros processos de corte térmico (ou termoquímico) mais
adequados. Para peças em aço carbono, com espessuras acima de
A figura 14 mostra a
relação
de aplicação entre os p
rocessos de corte térmico.
Neste artigo procuramos elucidar as características e aplicação e as diferentes formas do processo plasma. Porém é sempre recomendada uma sucinta avaliação para cada aplicação, envolvendo os critérios de exigências de qualidade dimensional da chapa, qualidade da superfície de corte, produtividade, investimento e custo operacional para se definir o processo de corte mais adequado.
Fonte: Erasmo G. Lima - Hypertherm
a) insumo para geração do plasma
b) refrigeração dos consumíveis.
Ainda, nos sistemas com partida por contato, serve como agente para afastar o eletrodo móvel.
Anteriormente vimos que o plasma é gás aquecido por uma diferença de potencial elétrico. Portanto, a qualidade e eficiência do processo estão intrinsecamente relacionadas com a qualidade do gás. Na grande maioria dos sistemas manuais, utiliza-se uma única fonte de suprimento de gás para realizar as duas funções de formação de plasma e refrigeração dos itens consumíveis. Neste caso a vazão do gás torna-se um fator de extrema importância para o desempenho do processo. Se a vazão é excessiva implicará numa boa ação de refrigeração, porém com conseqüências danosas ao plasma. Se insuficiente, além da perda de qualidade do plasma, a vida útil do consumível é reduzida drasticamente. A vazão nos sistemas de gás único e sempre mais elevado que nos sistemas de
múltiplos gases. Existem alguns sistemas manuais, de correntes mais elevadas que podem utilizar a combinação de mais de um gás. Em conseqüência tem-se uma tocha mais robusta e pesada. Os sistemas mecanizados dedicados possibilitam o uso de dois gases distintos para plasma e para proteção. Nestes casos, o eletrodo é refrigerado internamente por um líquido refrigerante. A vantagem dos sistemas múltiplos gases está no fato de selecionar um gás de plasma mais adequado ao tipo de material a se cortar independente de sua capacidade de refrigeração. As tabelas 1a e 1 b mostram respectivamente as características recomendações para gás de plasma e de proteção. A seleção deve se dar primeiramente para atender aos requisitos de qualidade e produtividade do material a se cortar. O Ar comprimido é sempre a melhor segunda opção técnica e a primeira
em conveniência e custo. Quando se deseja a melhor combinação para obter melhor qualidade e produtividade, os gases recomendados são mostrados na tabela.
PLASMA DE ALTA DEFINIÇÃO
A definição ou qualidade de corte é caracterizada pelo desvio e angularidade da superfície de corte. A norma ISSO 9013 estabelece critérios de avaliação com base na espessura do material conforme mostrado na tabela 3. Os níveis vão de
O processo plasma de alta definição foi criado com o objetivo de produzir cortes com qualidade nível 3. Porém em produção, com as constantes variações de pressão e vazão nos gases de plasma e proteção, aliado ao desgastes da tocha e dos consumíveis, o processo se mantinha com nível de qualidade entre o 4 e 5 e uma vida útil do bico e eletrodo de aproximadamente 2 horas. Por este fato o processo tendia ao colapso na sua utilização para a indústria devido ao alto custo operacional e baixa consistência. Em 2003 foram investidas elevadas quantias em pesquisa e desenvolvimento para resolver a inconsistência e aprimorar o processo de alta definição. O resultado foi o desenvolvimento de duas novas tecnologias que revolucionaram o plasma de alta definição. Um controle sinérgico para o gás e um novo desenho de tocha que permite a flutuação do tubo de refrigeração dentro do eletrodo proporcionou a consistência do processo, ou seja, produção de cortes com qualidade nível 3 por um longo período de vida dos consumíveis bico e eletrodo. O processo que foi batizado de Hyperformance, ou plasma de Alto Desempenho, já é comercializado desde 2004 e os resultados médios comprovam a qualidade nível 3 em uma vida útil de eletrodo
e bico em média de 6 horas. A figura 13 mostra algumas peças cortadas com processo de alta definição.
Fonte: Erasmo G. Lima - Hypertherm
Os sistemas de corte manual são muito simples e de fácil operação. Os sistemas mais modernos possuem o bocal isolado eletricamente o que permite que o operador apoie a tocha na peça e/ou utilize uma régua ou gabarito para guiar o corte. As fontes inversoras são preferidas devido a sua a portabilidade. O corte manual é largamente utilizado nas mais diversas aplicações. Desde cortes em chapas finas como as de automóveis ou móveis, até grandes espessuras como as de estruturas metálicas, o plasma apresenta vantagens devido a flexibilidade da tocha, facilidade de operação, velocidade de corte e menor deformação das chapas.
Corte Mecanizado
Corte mecanizado é todo aquele onde um sistema automático manipula a tocha de plasma. Os
Sistemas pode ser simples como uma “tartaruga” ou até os mais complexos manipulados e comandados por CNC. Os sistemas manuais podem ser adaptados para trabalhar no método mecanizado e devem ser respeitados os limites de aplicação recomendados pelo fabricante
do sistema para este método. Geralmente a capacidade de corte dos sistemas manuais é reduzida à metade para o corte mecanizado. Esta redução não está relacionada diretamente com a capacidade da fonte, e sim pelo aquecimento progressivo da tocha. Como no plasma a velocidade reduz sensivelmente com o incremento da espessura, em chapas mais espessas o tempo de corte é grande devido a baixa velocidade. Esta é a principal razão de se limitar a espessura para se garantir uma velocidade razoável e permitir o refrigeração adequada da tocha. Os sistemas mecanizados dedicados geralmente possuem tochas refrigeradas por líquido refrigerante. O liquido é guiado na parte interna do eletrodo permitindo um jato de líquido exatamente na parte traseira do ráfnio – parte que fica no estado líquido durante o corte.
Um sistema básico mecanizado é constituído por 5 partes principais conforme mostrado na figura11
1.Fonte de Energia
2.Console de Ignição – Alta Freqüência
3.Console de controle de gás
4.Tocha plasma
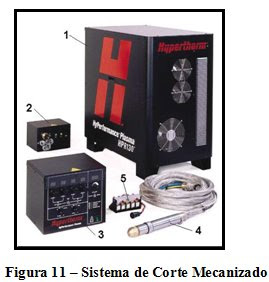
Este conjunto é parte integrante de uma célula ou máquina de corte. A qualidade do corte, bem como o desempenho da célula depende da combinação, interação e características dos componentes como: Sistema de Corte Plasma – os 5 itens mostrados acima, Comando CNC, Controle de altura
(eixo Z) e Sistema de movimentação X-Y. A figura 12 mostra um exemplo de máquina de corte com comando CNC e os itens componentes

Fonte: Erasmo G. Lima - Hypertherm
Introdução
Os 3 primeiros estados da matéria são sólido, líquido e gasoso. Em exemplo, usando uma das mais conhecidas substâncias, a água (H2O), estes estados são: gelo, água e vapor. Quando a energia, como calor, é aplicada ao gelo, o gelo se derrete se tornando água. A água se transforma do estado sólido, gelo, para o estado líquido, água. Quando mais energia é aplicada à água, a água vaporiza tornando-se vapor. A água (H2O) muda do estado líquido, água, para o estado gasoso, vapor (H2 & O2). Finalmente, quando calor é aplicado aos gases, estes gases ionizam. Os gases agora são eletricamente condutores e este estado da matéria é chamado plasma. A figura 6 mostra esquematicamente esta seqüência. O constantemente denominado “4º estado da matéria”
é chamado PLASMA. Este gás ionizado com propriedades é a base fundamental em que todos os sistemas plasma operam.
Definição de Plasma
“Uma coleção de partículas carregadas contendo quase a mesma quantidade de elétrons e íons positivos, e, embora apresente quase todas as características dos seus gases formadores, se difere deles por ser um bom condutor de eletricidade”. A ionização do gás causa a criação de elétrons livres e íons positivos entre os átomos de gás. Quando isso ocorre, o gás em questão torna-se eletricamente condutivo com excelente capacidade para transmissão de corrente elétrica. O melhor exemplo de plasma na natureza é a tempestade de raios. Exatamente como na tocha plasma, os raios movem à eletricidade de um ponto a outro. Para o raio, os gases do ar são os gases ionizados.
Corte Plasma
O corte a Plasma é um processo que utiliza um bico com orifício otimizado para constringir um gás ionizado em altíssima temperatura, tal que possa ser usado para derreter seções de metais condutores. Um gás eletricamente condutivo (plasma) é usado para transferir energia negativa fornecida pela fonte plasma da tocha para o material a ser cortado (obra). A tocha serve de suporte para os consumíveis e fornece um fluído refrigerante para estas peças (gás ou água).
O distribuidor ou difusor de gás é construído de material isolante e tem como principal finalidade de dar sentido rotacional ao gás. O eletrodo conduz a corrente até um inserto de háfnio que emite os elétrons para geração do plasma. O bico constringe o plasma e o guia para o metal a ser cortado. A capa tem como função manter os consumíveis alinhados e isolar a parte elétrica do bocal frontal. O bocal frontal guia o fluxo de jato de ar coaxial. Por ser refrigerado e isolado, o bocal pode ser apoiado à chapa.
Seqüência de Operação
Um sinal de partida (START) é enviado a fonte plasma. Simultaneamente a tensão de arco aberta (OCV) e os gases são transmitidos à tocha. Quando a vazão é estabilizada, a alta freqüência (HF) é ativada. A HF aparece entre o eletrodo e o bico dentro da tocha e o gás se ioniza ao passar pelo arco. Este gás eletricamente condutor cria um caminho para corrente entre o eletrodo e o bico e dele, resulta a formação do arco piloto. Quando o arco piloto consegue contato com
a obra, ele é transferido à obra. O arco plasma funde o metal e o gás em alta velocidade remove o
metal derretido.
Métodos de Partida
Partida por contato:
O eletrodo e bico estão em contato (“curto-circuito”) e conectados a fonte plasma. A pressão de gás faz se distanciarem o bico e o eletrodo, criando um arco. Este arco (piloto) é auto-sustentável (corrente CC); Este tipo de partida é encontrado em muitos sistemas pequenos.
Partida por alta freqüência:
Alta tensão elétrica (de
método é utilizado nos sistemas com eletrodo refrigerado por líquido. Apesar de ser utilizado na maioria dos sistemas plasma, oferece o inconvenientes por causar ruídos na rede elétrica requerendo um aterramento eficiente para proteção principalmente de equipamentos eletrônicos instalados próximos ao equipamento ou mesmo nas máquinas de corte.
Fonte: Erasmo G. Lima - Hypertherm
Introdução
Desde sua invenção na metade da década de 50, o processo de corte por plasma incorporou várias tecnologias e se mantém como um dos principais métodos de corte de metais. Porém, até poucos anos atrás, o processo detinha uma reputação duvidosa na indústria de corte de metais devido ao elevado consumo dos itens componentes do sistema, o ângulo de corte e a
inconsistência do processo. Os recentes desenvolvimentos agrupando tecnologias
em sistemas de cortes manuais e mecanizados, proporcionaram um marco importante na história do
corte plasma.
Os plasmas manuais mais modernos são equipados com sistema de jato coaxial de ar, que constringe ainda mais o plasma, permitindo um corte mais rápido e com menos ângulo. O projeto de escuto frontal permite ao operador apoiar a tocha na peça mesmo em correntes elevadas na ordem de
dos componentes consumíveis através de um controle mais eficiente dos gases e do sistema de refrigeração respectivamente.
O processo de corte plasma, tanto manual como mecanizado
ganhou espaço considerado na indústria do corte de metais. Mesmo descontado o crescimento
desta indústria, a participação do corte plasma teve substancial ampliação devido a sua aplicação em substituição ao processo oxi-corte, em chapas grossas, e ao LASER em chapas finas ou de metais não ferrosos. Neste artigo iremos revisar a evolução do desenvolvimento tecnológico, a teoria do processo de corte plasma, os detalhes de processos e procedimentos, além da relação comparativa com os demais processos de corte térmico.
Resumo Histórico
O processo de corte plasma foi criado na década de 50 e tornou-se muito utilizado na indústria devido sua capacidade de cortar qualquer metal condutor de eletricidade
principalmente os metais não ferrosos que não podem ser cortados pelo processo oxi-corte. O
processo consiste na utilização do calor liberado por uma coluna de plasma, resultante do aquecimento– por maio de um arco elétrico - de um gás, em alta vazão rotacional. Este plasma é transferido ao metal a ser cortado. A parte do metal se funde pelo calor do plasma e este metal é expulso com auxílio do gás em alta vazão. A figura 1 mostra os detalhes do corte plasma.
Em 1968 surge a primeira grande inovação, a injeção de água entre o bico e um bocal frontal, com o
objetivo de ampliar a vida útil dos consumíveis e na qualidade de corte, conforme figura 2
Em 1983 torna-se industrialmente viável a utilização do plasma com oxigênio para materiais ferrosos. Com o oxigênio como gás de plasma o calor do processo provém de duas fontes: a do plasma e da reação exotérmica da oxidação do ferro. A resultante é um aumento considerável de velocidade e qualidade de corte. Em 1989 lança-se o bocal protetor eletricamente isolado
Para melhorar a vida útil dos consumíveis, principalmente nos processos com o uso do oxigênio como gás de plasma, em 1990 são incorporadas seqüências lógicas nos sistemas plasma
com ajustes específicos de corrente e vazão e pressão de gás nos intervalos de início e final de corte, conhecido como tecnologia LongLife. Esta tecnologia conta ainda com o aprimoramento do projeto do eletrodo. Com um inserto de ráfnio de menor diâmetro, amplia-se a capacidade de refrigeração do eletrodo. Nesta mesma época surge o plasma de alta definição (figura 4) que revoluciona o processo plasma e o torna aplicável em peças com maiores exigências de qualidade de corte. O processo utiliza um orifício reduzido no bico e um canal extra para saída de excesso de gás plasma resultando num corte praticamente sem chanfro e sem geração de escória.
Em 1993 é lançado o processo com jato de ar auxiliar aplicado coaxialmente ao jato de plasma (figura 5). Esta força de constrição aumenta a eficiência do jato proporcionando um aumento de velocidade e redução do ângulo de corte. Em 2004 são incorporadas novas tecnologias ao processo
plasma de alta definição com o objetivo de melhorar o desempenho e consistência do processo.
O resultado foi a criação do processo HyPerformance ou plasma de alto desempenho. Com todo este avanço tecnológico, o plasma torna-se um dos processos mais importantes na indústria do corte do país. Atualmente o plasma vem sendo usado tanto para acompanhar o crescimento da indústria, bem como na substituição de processos mais lentos ou com maiores custos operacionais.
A seguir iremos estudar em detalhes, características e aplicação do corte plasma.
Fonte: Erasmo G. Lima - Hypertherm
Postagens mais recentes Página inicial